EC-04, STRONGLY ENGINEERED
EC-04, The renewal
After a last laborious project and performances below the expected results, the ESTACA Formula Team had to reinvent itself to survive and return to the forefront.
The EC-04 project began in September 2021, in a difficult economic context for the association. Indeed, we had reached a particularly low number of members and lost a large number of our partners following the covid period.
Only a handful of students remained from the previous year with the knowledge and the desire to develop a single-seater marking a new page in the history of the association.
We therefore developed EC-04 by wanting it to be simple in its design and technologies but professional in its development and manufacturing. We also had to get closer to the standard production rates of the Formula Student. For this we chose to produce this single-seater over a period of 2 years.
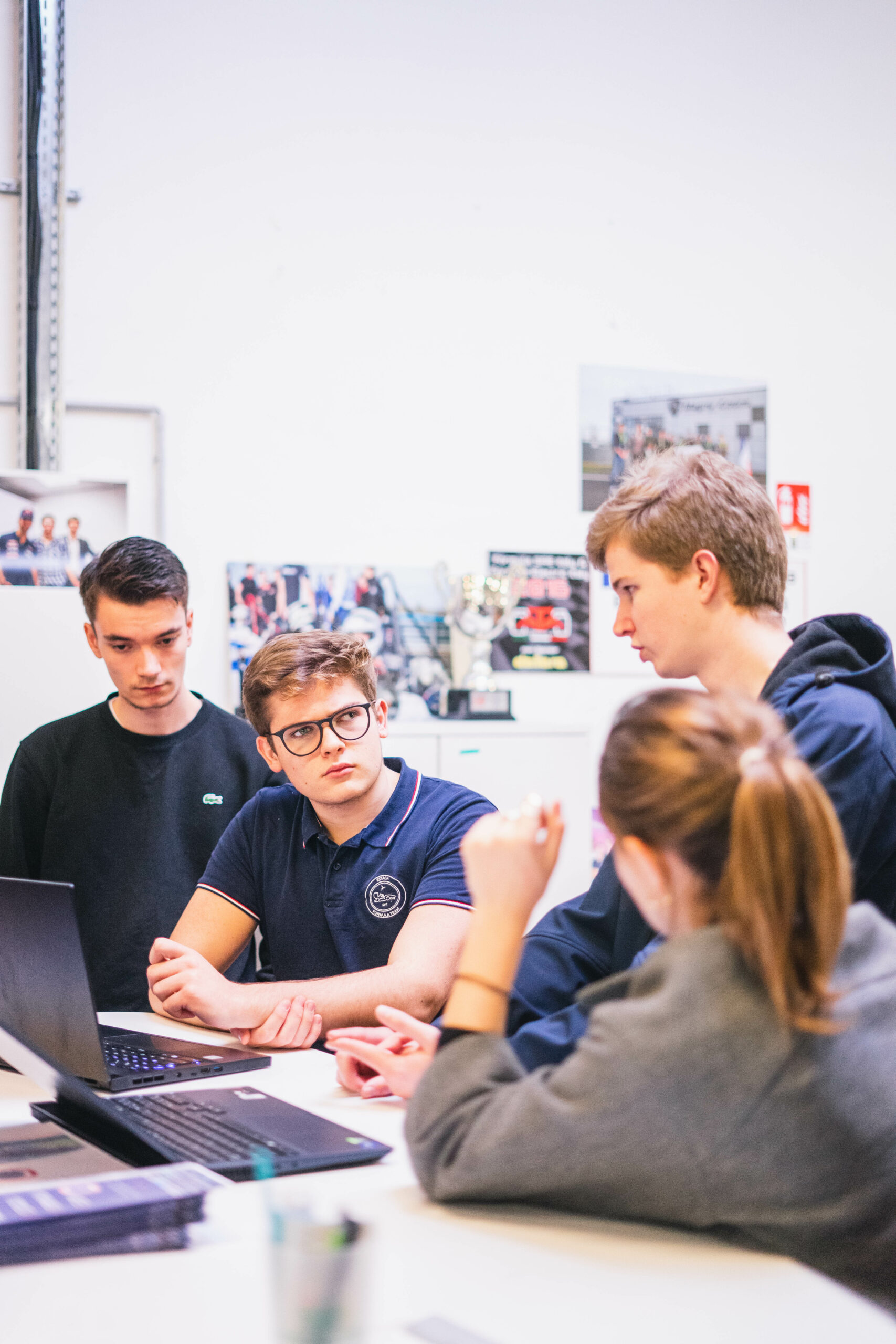
SIMPLICITY SERVING PERFORMANCE
Given our resources at the time of launching the project, we could not afford to choose the cutting-edge technologies used on the previous single-seater, which were too expensive and complex to implement for this renewal. The simplicity of the systems and the thought of the processes necessary for manufacturing were the number one challenges of our design process. This simplicity should also allow us to obtain a healthy single-seater that would represent a good working basis for the association’s future vehicles.
As part of this simplification, we chose to return to a tubular chassis, which is easier to develop and manufacture, and to keep the same powertrain to capitalize on the achievements of the previous generation and to be able to work on its reliability.
The chassis: back to the origins
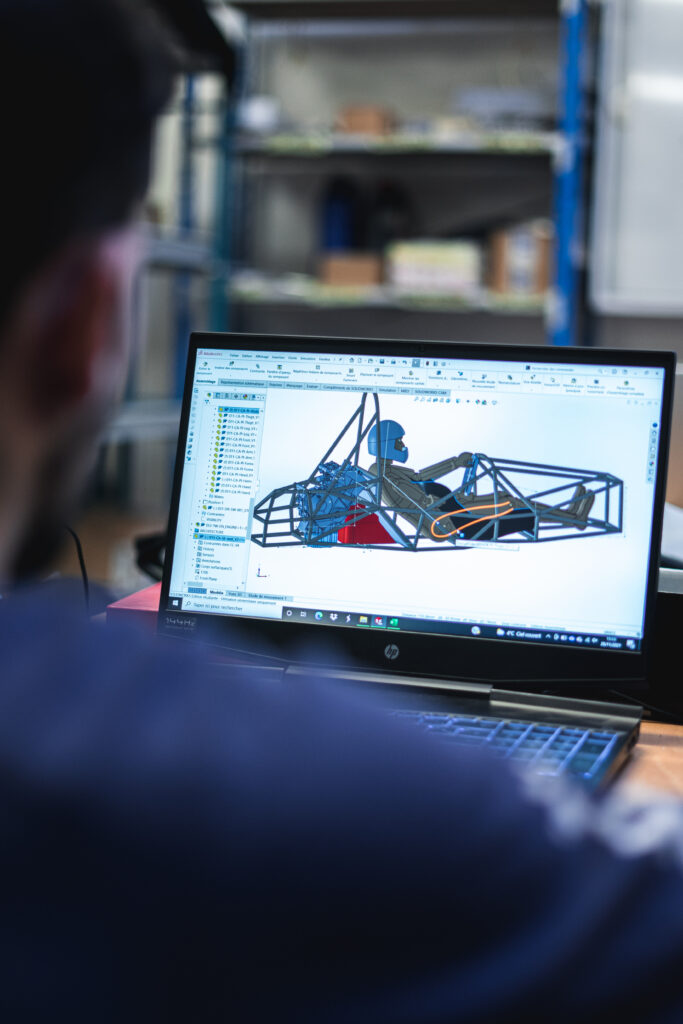
To develop the EC-04 chassis, we started from the chassis of its big sister EC-02 to give us the main guidelines.
Many projects were conducted in parallel by the Chassis division in order to develop a new tubular that meets all of our needs: ergonomics for the driver, safety crashbox and crash test, analysis of rigidity and weight reduction and manufacturing methods (all of these elements must comply with the particularly strict Formula Student regulations).
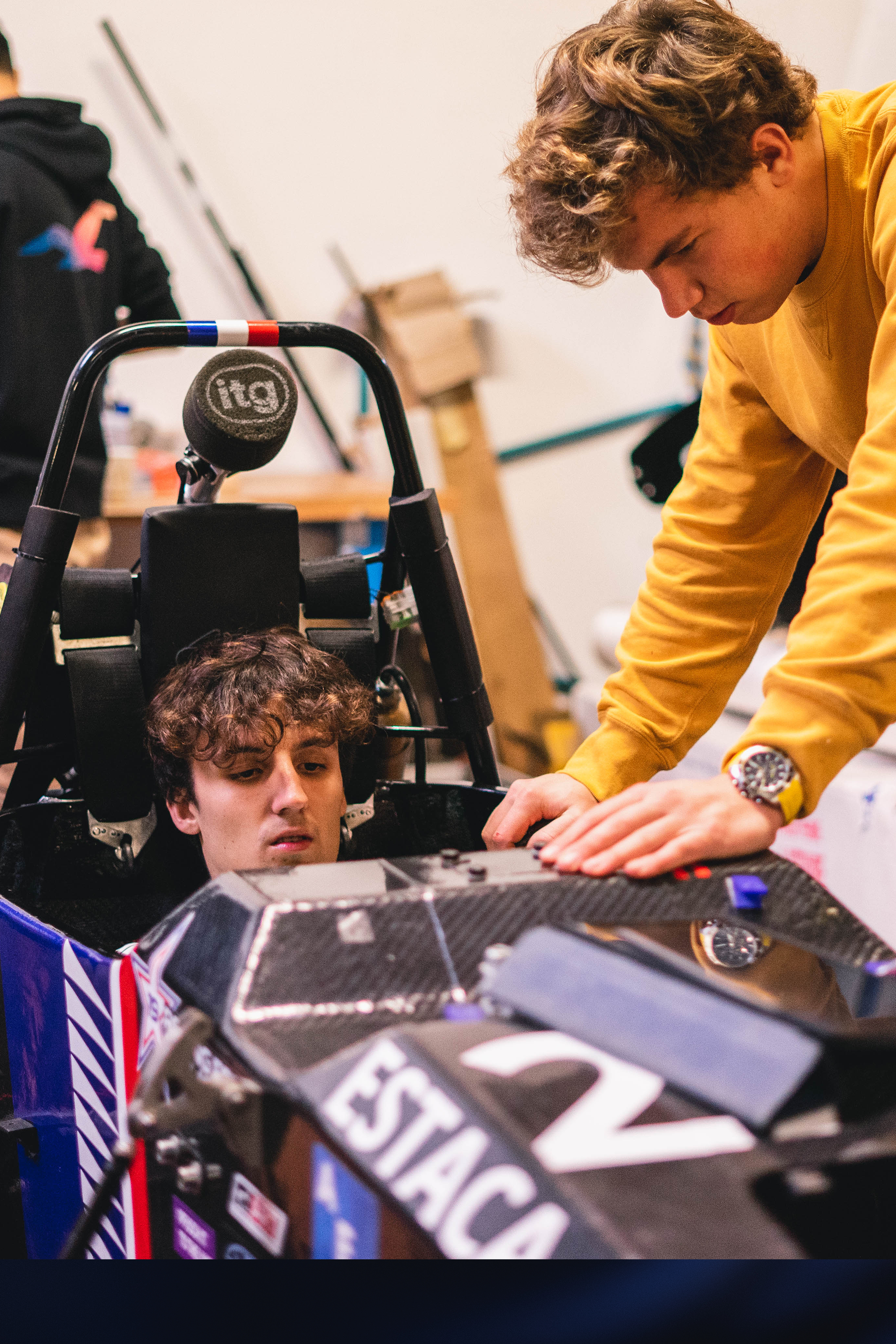
To develop a Formula Student chassis, you must first choose the anchor points for our Ground Connections. Then the Chassis department takes care of connecting these points while leaving enough space for the other parts of the vehicle, such as the engine but also the driver.
To maximize performance, we want this chassis to be as rigid as possible, but also light, two variables often evolving in the same direction. It is therefore necessary to define a stiffness objective and then make compromises on either one or the other throughout the development.
To help us in our approach, we used Ansys Mechanical to simulate different configurations of our chassis and thus determine the best compromise.
We would like to particularly thank FASTER for their support in this project, without whom we would not have been able to weld our tubes. We were able to benefit from state-of-the-art equipment for positioning our tubes and the help of their team of welders to manufacture a chassis that is precise to within 0.2mm.
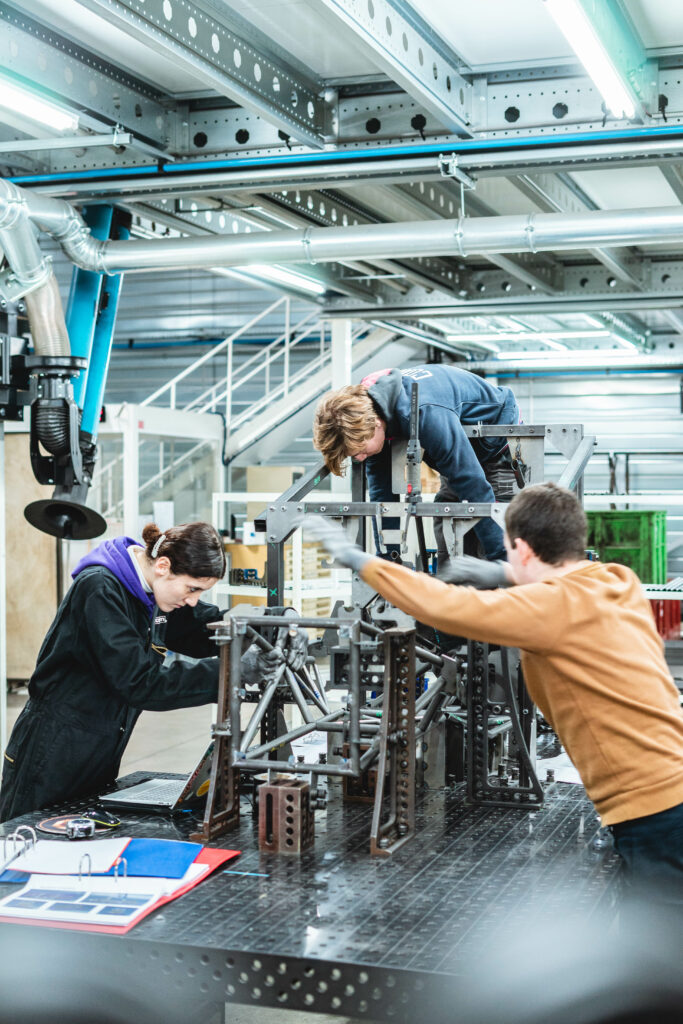
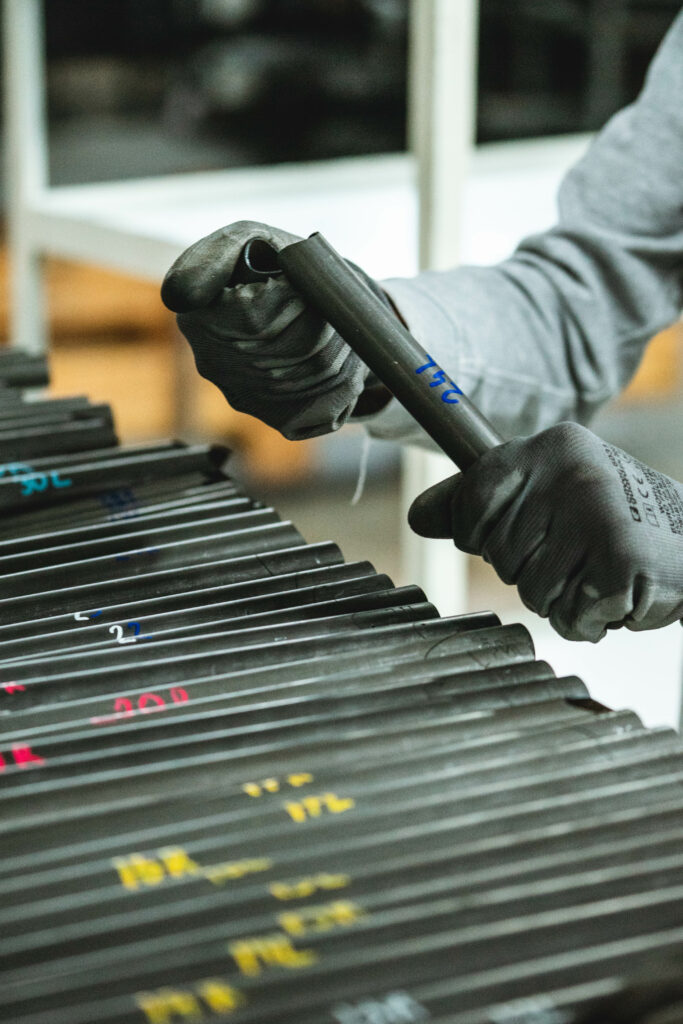
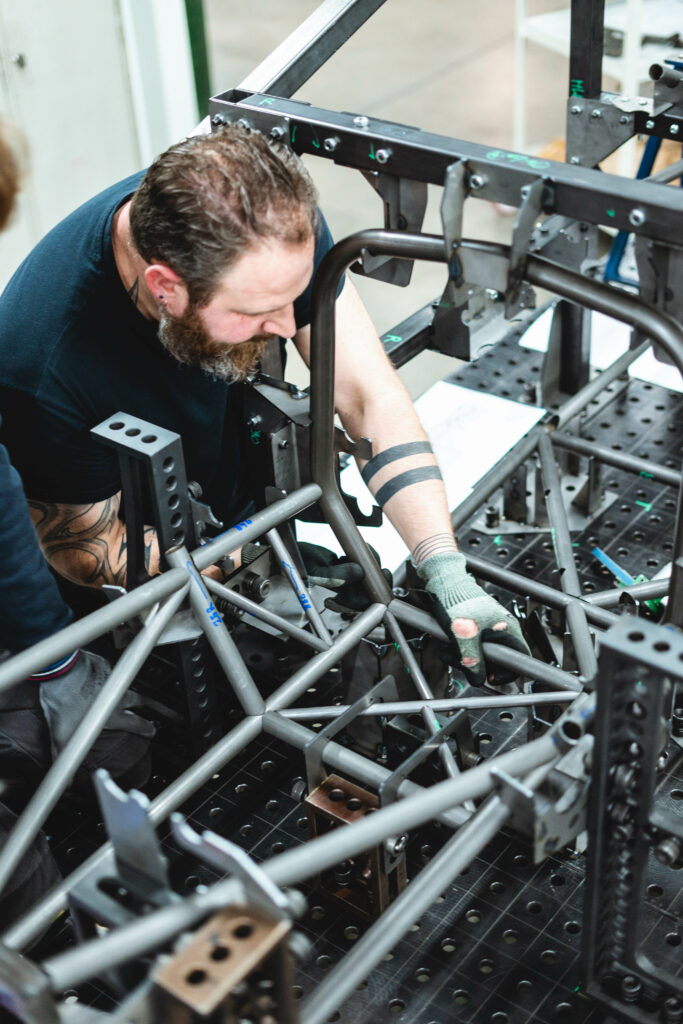
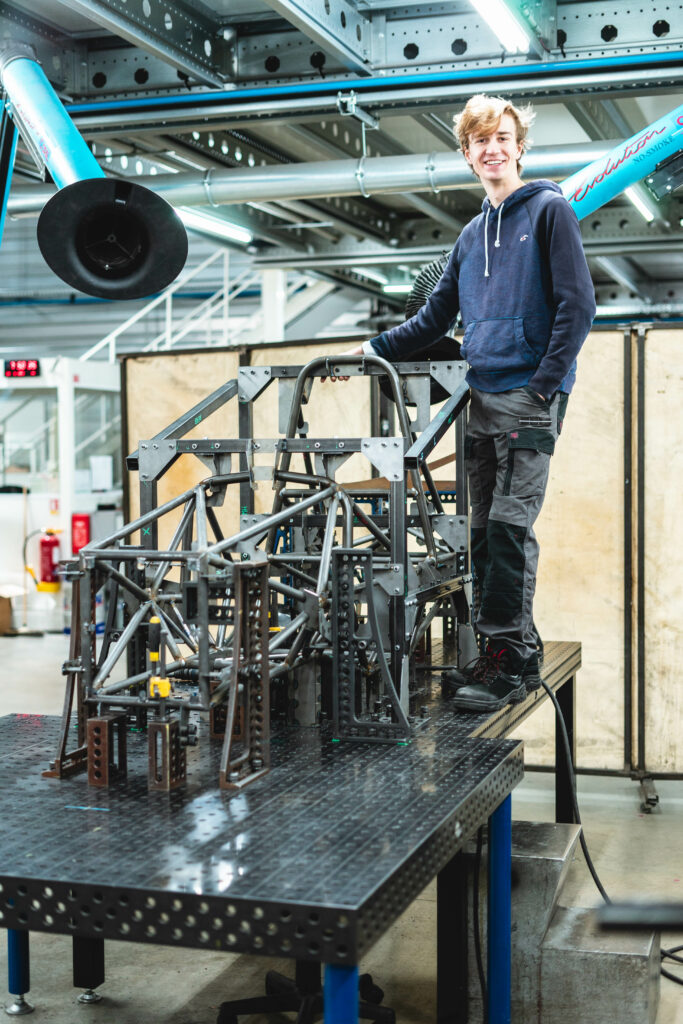
The powertrain: continuity
We chose to keep the same engine/differential assembly for EC-04 in order to capitalize on the lessons learned from the previous vehicle. In addition, the performance of the latter had satisfied us.
For this vehicle, we therefore worked on improving its performance. We want to extract more power from it. With this objective, we worked on optimizing the intake. We also worked on optimizing the air flow in the air box using the resonance phenomenon.
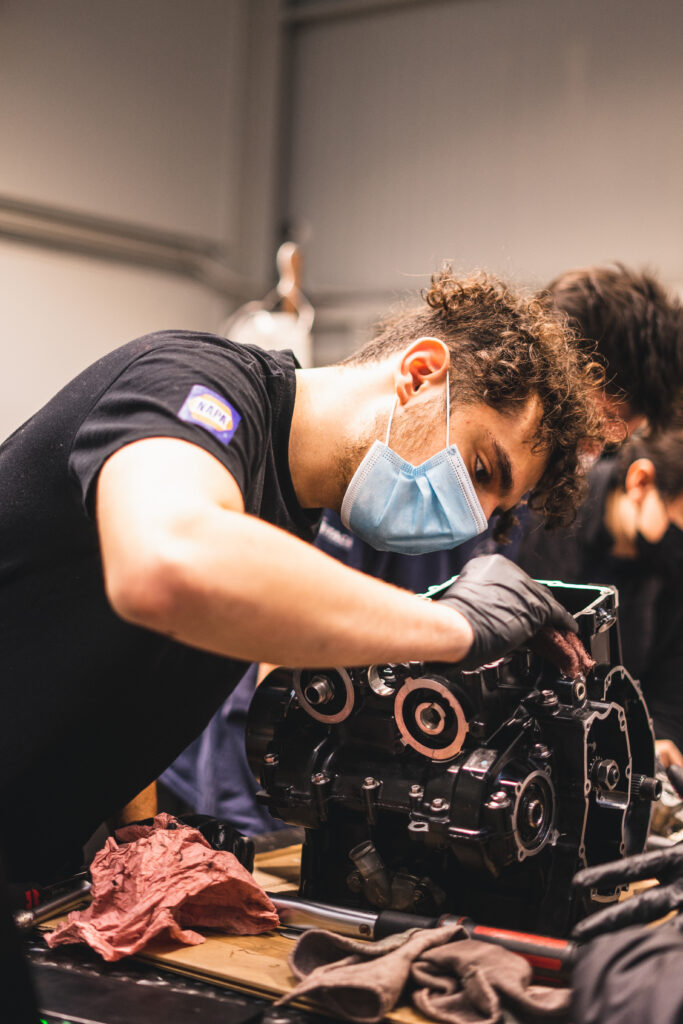
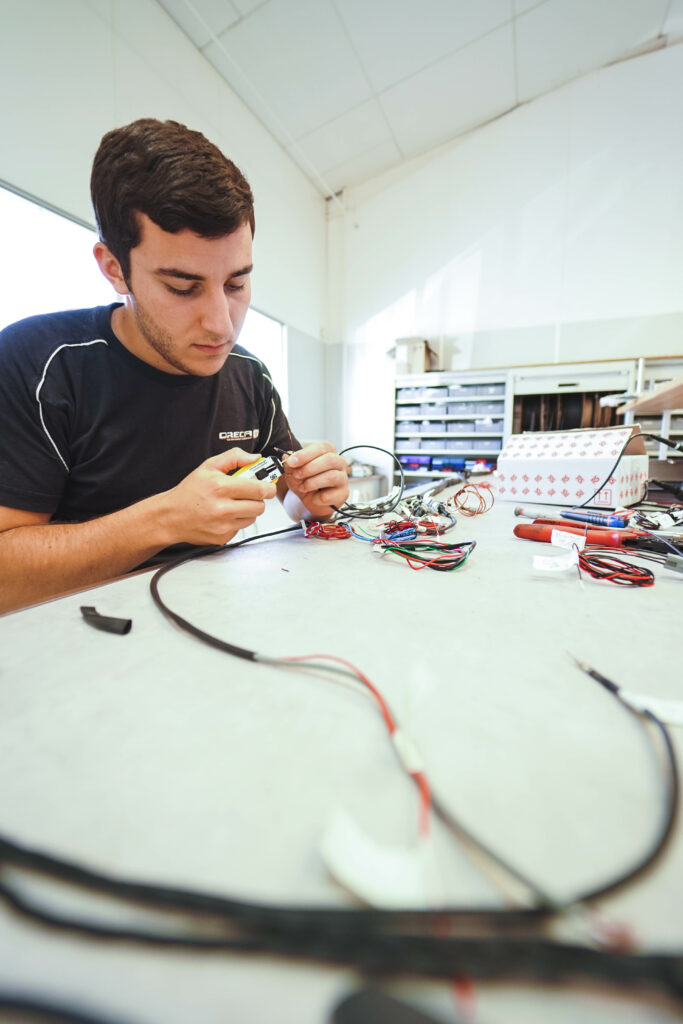
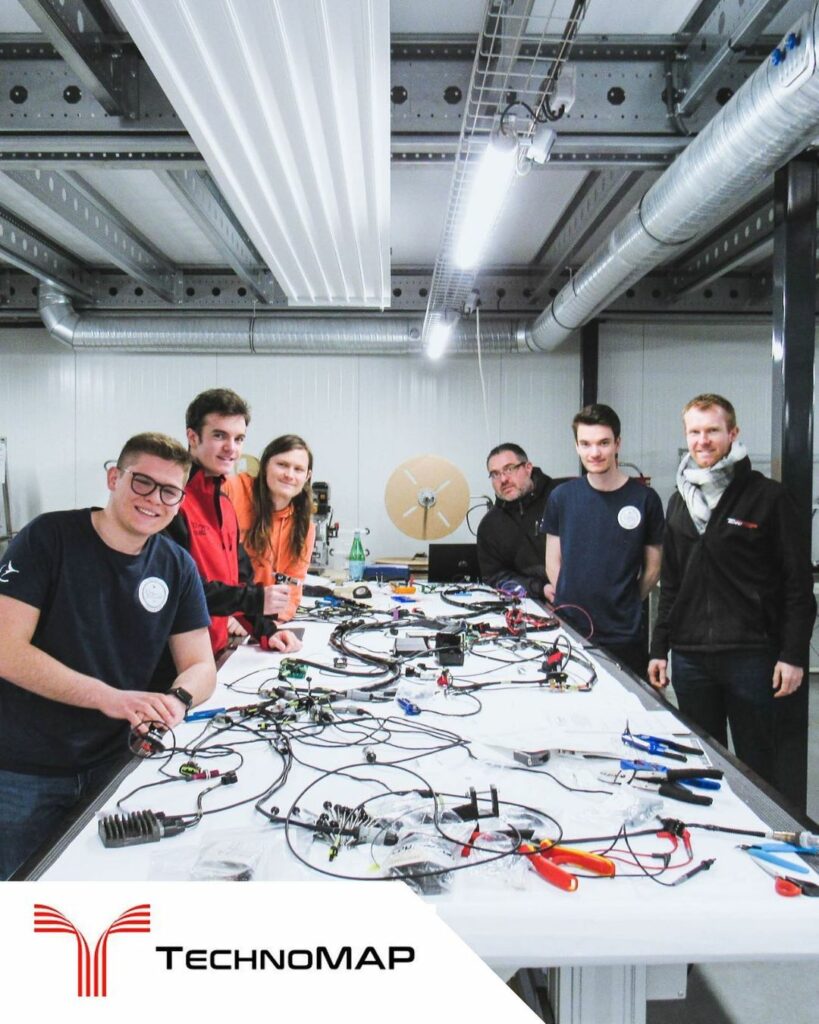
As for the beam pole, working very closely with the GMP pole, their job was to significantly improve the reliability of the single-seater’s electronics, before being able to set up more complex control and data acquisition systems.
To do this, they completely redesigned the single-seater’s electrical circuit. We were able to benefit from the help of Technomap and Oreca for its design and manufacturing. This collaboration allowed us to set up professional-level design and manufacturing processes, limiting the risks of error and malfunction.
The aerodynamic pole: efficiency
For EC-04, the primary objective was to improve the efficiency and reduce the mass of our aerofoils. This requires a much better manufacturing quality than that of our first aerodynamic pack (on EC-03). We then had to redesign our pack in order to define simpler geometries, adapted to our production capacities. This design cycle was therefore marked by numerous iterations of our concept in CFD.
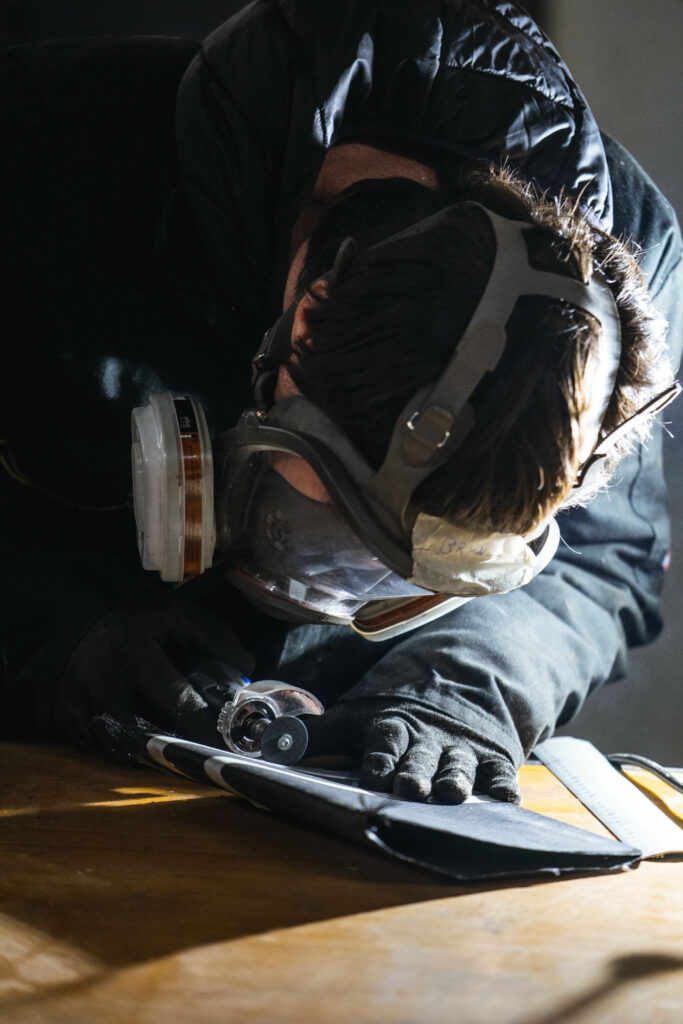
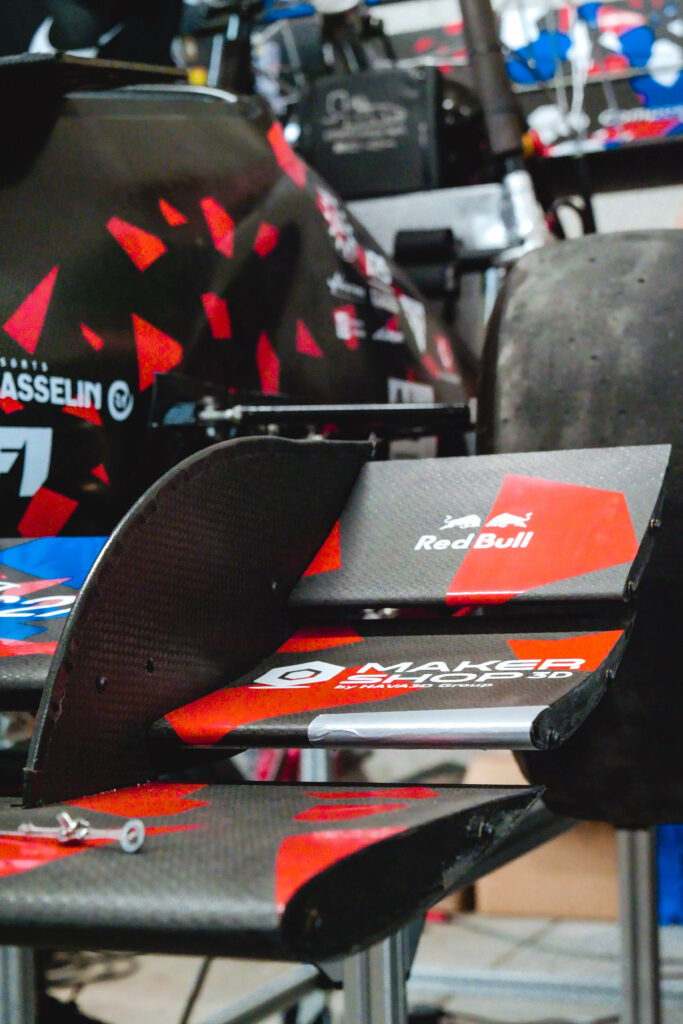
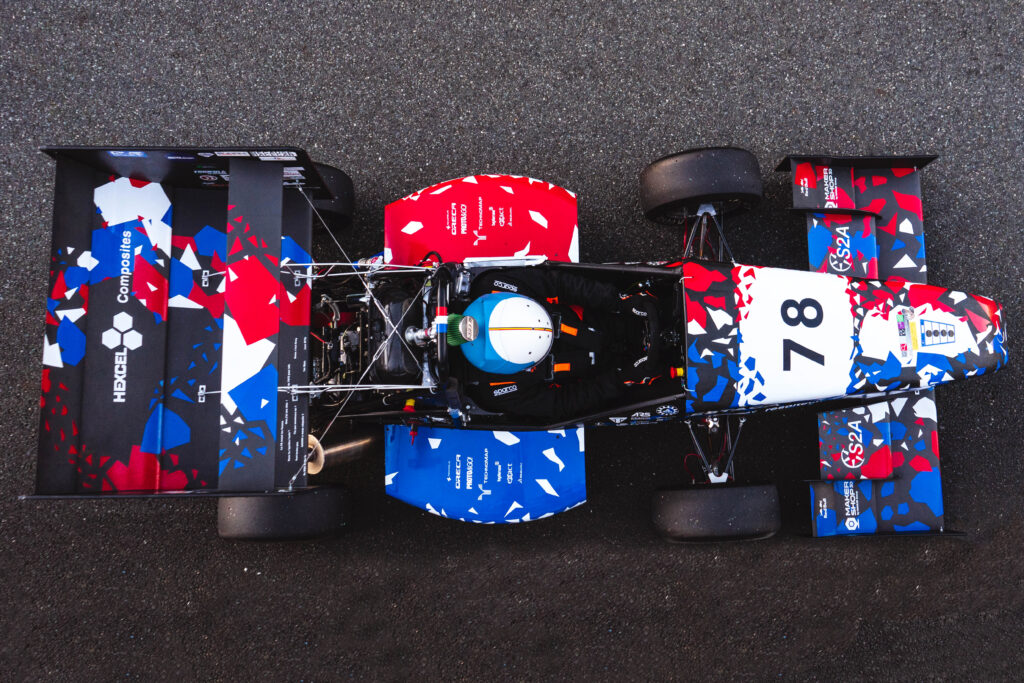
Ultimately, after extensive research into manufacturing methods, we managed to achieve a mass reduction of almost 18 kg compared to the previous year thanks to the use of geometry adapted to our capabilities, resulting in an aerodynamic package made almost entirely of carbon fibre.
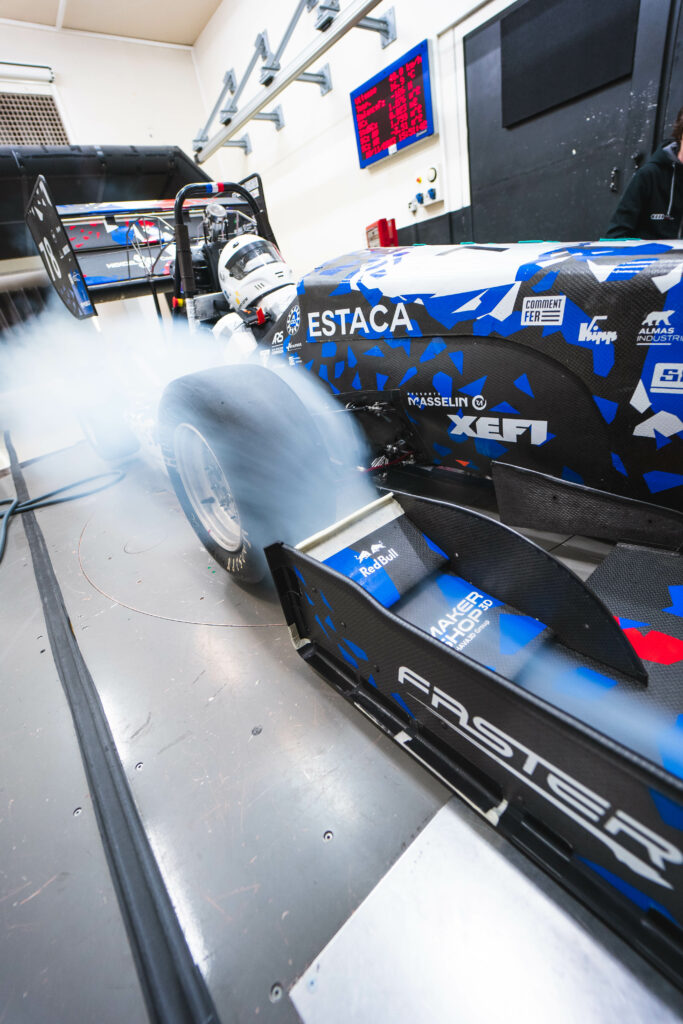
We were also fortunate to be able to conduct a wind tunnel test at our partner S2A in order to correlate with our simulation results. This was an extremely enriching experience for the team, allowing us to identify the strengths, but also the weaknesses of our aerodynamic concept.
The EC-04 aerodynamic package was a good success since we reached a downforce of 1220 Newtons at 100 km/h in the wind tunnel, which represents only a deviation of 03% compared to the simulations.
These results are encouraging for the continuation of the association, constitute a good basis for aerodynamic improvements, contributing to the performance of the single-seater.
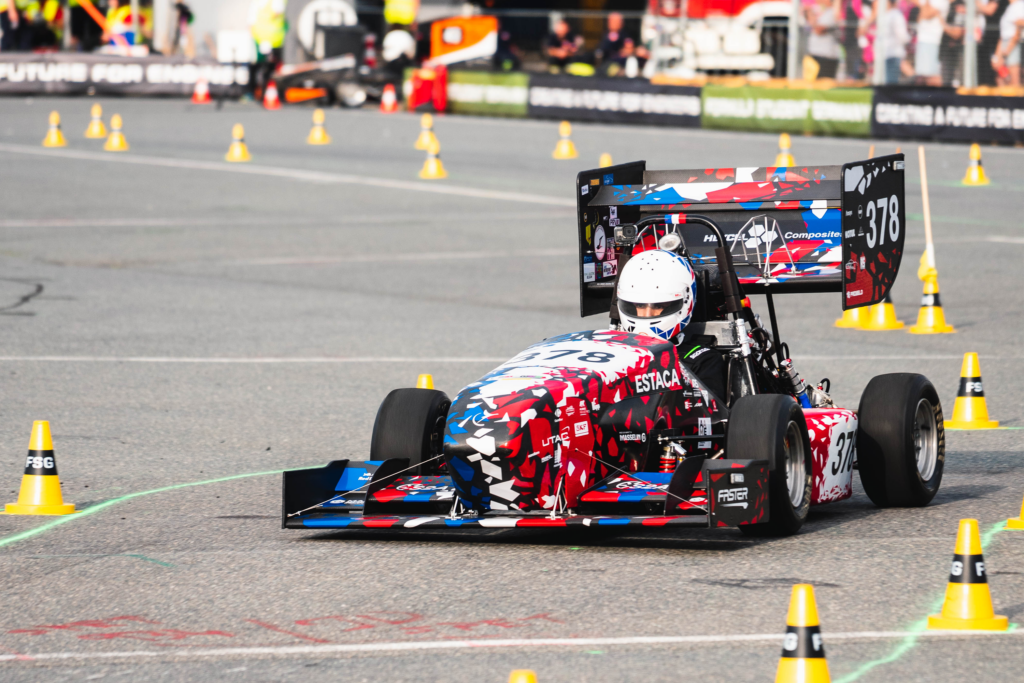
The final goal: competitions
Every summer, around fifteen competitions take place across Europe where teams from all over the world come together to compete in the biggest design competitions in the world.
This year we qualified for Formula Student Germany and Formula Student East, which are among the 3 most prestigious in the world.